5 Ways Enterprise Mobility Enhances Quality Control in Manufacturing
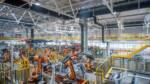
Every industry over the past few years has adopted enterprise mobility technology on a temporary or permanent basis, but some industry sectors have found more pronounced, defined benefits than others.
The concept of enterprise mobility is where the integration of mobile technology, cross-platform applications, and cloud services allows workers who do not work primarily at a stationary desk to work on the move while maintaining access to all of the data they need to maximize their productivity.
One of the industries that has reaped the biggest benefits of enterprise mobility is manufacturing. Mobility systems are a vital part of the manufacturing transformation often known as Industry 4.0 or the Fourth Industrial Revolution. The use of advanced analytics, cloud data and applications, as well as the Internet of Things (IoT) in the production process, has led to improved quality control systems and workflows that have helped improve efficiencies in production processes. And, with many manufacturing businesses now focused on lean manufacturing, the concept of minimizing waste while optimizing productivity and efficiency, improving quality control becomes paramount.
Here are five of the main ways enterprise mobility has meant better quality control in the manufacturing sector.
Real-Time Data Access
The key part of enterprise mobility in manufacturing is an interconnection between the machines and processes that help produce products and the devices used by people tasked with not only managing the machines but also interpreting the vast amount of data that a major industrial process will inevitably produce every day.
A shop floor is inevitably some distance away from the business intelligence departments that require as much relevant data as possible to develop trends, interpret patterns, and identify the health of the business using a variety of different sets of data from every part of the business.
Historically, this has been exceptionally difficult to do and almost impossible to coordinate without exceptional effort and discipline. However, through the use of UC (unified communications) tools and mobile technology, this has become far easier to consolidate and for users to access wherever they are, whether that is at a desk or on the move.
This information helps to create real-time, accurate maps of data that can be used by stakeholders and business leaders to make critical decisions with as perfect access to data as possible, improving their capacity to make the right business decisions. For example, factories can measure different historical trends for demand and production, along with current sales and logistic trends to see how much product they need to produce and how long it would take to ramp up production in cases of high demand before more product reaches shelves. It also can be used to model how long it will take to enact changes in a manufacturing pipeline if quality control notices a potential defect.
Enhanced Communication and Collaboration
One of the most universal benefits of enterprise mobility is how it brings people together no matter how physically distant. Mobile technology like enterprise smartphones or DECT solutions allows for much faster and more reliable forms of communication while also making communication like email or video conferencing that was previously only available to desk-based workers accessible by deskless workers like those on the manufacturing floor.
These collaboration and communication tools, which range from systems such as group message boards, project management tools and video conferencing applications to more specific and specialized bespoke software, bring forth the power of the collective.
Data and files stored on the cloud can be accessed and edited by multiple people at the same time, allowing for collaboration on reports, real-time editing and ensuring that all employees are on the same page, regardless of where they are physically located.
With regards to quality control, it allows for faster escalation of potential issues to decision-makers and ensures that any unexpected breach of standards can be contained, controlled and rectified briskly.
Additionally, many workers on the factory floor previously had to rely on walkie talkies and overhead paging to communicate, which was incredibly difficult in noisy environments, and could often lead to information being misheard, or missed completely. Or, these deskless workers had to waste valuable time traveling to a workstation to receive and make phone calls. This can now be done via enterprise mobility devices, which leads to much better collaboration and communication. And these same devices used for calls can also be used to share data via UC tools, share photos for quality control purposes, access vital machine information, and so much more.
IoT Integration for Predictive Maintenance
The Internet of Things has fundamentally changed the lives and working practices of many people, but in manufacturing, the interconnected machinery, sensors and processes help to mitigate one of the greatest dilemmas in the industry: downtime. One of the bigger issues with manufacturing is the compounding effects of downtime. Machinery needs to be well-maintained, but to do so often requires the machines to have considerable downtime to ensure maintenance staff can safely examine systems. This can be exceptionally costly, not only for the work involved but also if the machines need to be turned off during times when they could be producing products, such as during peak demand for a particular good.
However, the alternative of dealing with machinery issues when they occur and causing a stop to the production process entirely is far worse and incurs a significantly greater cost. Mobility systems, particularly in the form of IoT sensors, can provide a perfect compromise; they allow for greater monitoring of machinery without the need for it to be shut off.
There are several ways in which IoT can be integrated into a factory floor to remove this issue entirely and allow for targeted, predictive maintenance schedules that only shut off and repair machines for a short amount of time as required. There are two processes that make this possible. The first is the integration of internal sensors that communicate not only with each other but with the wider IoT network, allowing for problems to be identified in real-time, even by people who are not currently on-site. And, with integration between these internal sensors that also send information and alerts to a mobile device, workers can be made aware of maintenance needs or problems with machinery anywhere and in real time, enabling faster responses.
Additionally, advanced sensors allow for the creation of a digital twin, which is a completely accurate virtual representation of a physical object, which in the case of a manufacturing plant would be a machine. A digital twin can be used to run models, simulations and long-term analysis and can help identify potential weaknesses and times when the system may require servicing. It can also factor in a myriad of different environmental factors such as humidity, temperature, performance and energy consumption to maximize the machine’s operation as much as possible.
All of this saves time, saves money and helps to avoid significant disruptions to a manufacturing business, where a delay can cause a huge ripple effect.
Mobile Quality Control Checklists/Digital Documentation and Reporting
Reporting protocols can often cause delays if there is a reliance on physical documentation. One of the most effective ways to save time is to streamline filling in a quality control checklist and submitting it into one simple virtual process. This is something that is exceptionally easy for a business mobility service to set up. Instead of relying on a clipboard, an inspector can use an enterprise smartphone to go through the entire inspection checklist, making notes on every aspect of a product.
Systems can also allow for much easier gathering of evidence and supporting material. For example, if a particular product or batch of products has a defect, an inspector can take a picture with their smart device and attach it directly to a checklist system with that functionality added to it. This can help to save huge amounts of time, both in reporting a potential issue that may require fixing before products can be sent to buyers, allowing for more rapid approvals, and ensuring that the product enters the supply chain faster than it might otherwise have been able to.
Having a systemic approach to inspection ensures a more consistent level of quality control, which in turn ensures better quality products that not only meet the expectations of customers but also exceeds them, leading to a better bottom line. It also allows for other digital documentation to be easily accessible using a cross-platform, cloud-based service like Microsoft Teams, ensuring a precise audit trail at every stage of the process.
Remote Monitoring and Analytics
The key strength of mobility systems is the ability for them to be used remotely, but the implication of just how beneficial this is cannot be overstated. All of the benefits pointed out above can be accessed from anywhere, at any time, by people who have secure access to the cloud-based systems involved. This means that if a quality control decision needs to be escalated, it can be brought up to someone who is not based in the same building, is a floating member of staff or is currently on the move, and they can access all of the information they need via mobile technology like an enterprise mobility solution to make a decision.
Access to analytics can help with stakeholder and pitch meetings to show an accurate representation of the business in real time, rather than relying on information that could be out of date by the time the business leader arrives at their meeting location. It also allows for much deeper levels of analytics information to be accessed anywhere, which means that it could be placed in the hands of a business intelligence specialist who may not be based in the same location as the rest of the organization. They can be provided with a secure link to access the information and interpret it without having to be in the same building, thus saving time, money, and ensuring an expert verdict can be rendered faster.
Conclusion
With manufacturing, time is money, and businesses no longer need to compromise either to maintain an extraordinarily high level of quality. Through enterprise mobility, appropriate team members maintain constant access to the machines, processes, information, and people they need to get the job done as accurately, efficiently, and timely as possible while maintaining quality standards. In an already complex state of the supply chain, and with an increasing demand on often overworked frontline mobile workers, mobile technology is now critical to success in manufacturing.
For more information on how Spectralink enterprise mobility solutions can help make your manufacturing workflows more efficient and LEAN, reach out to [email protected].